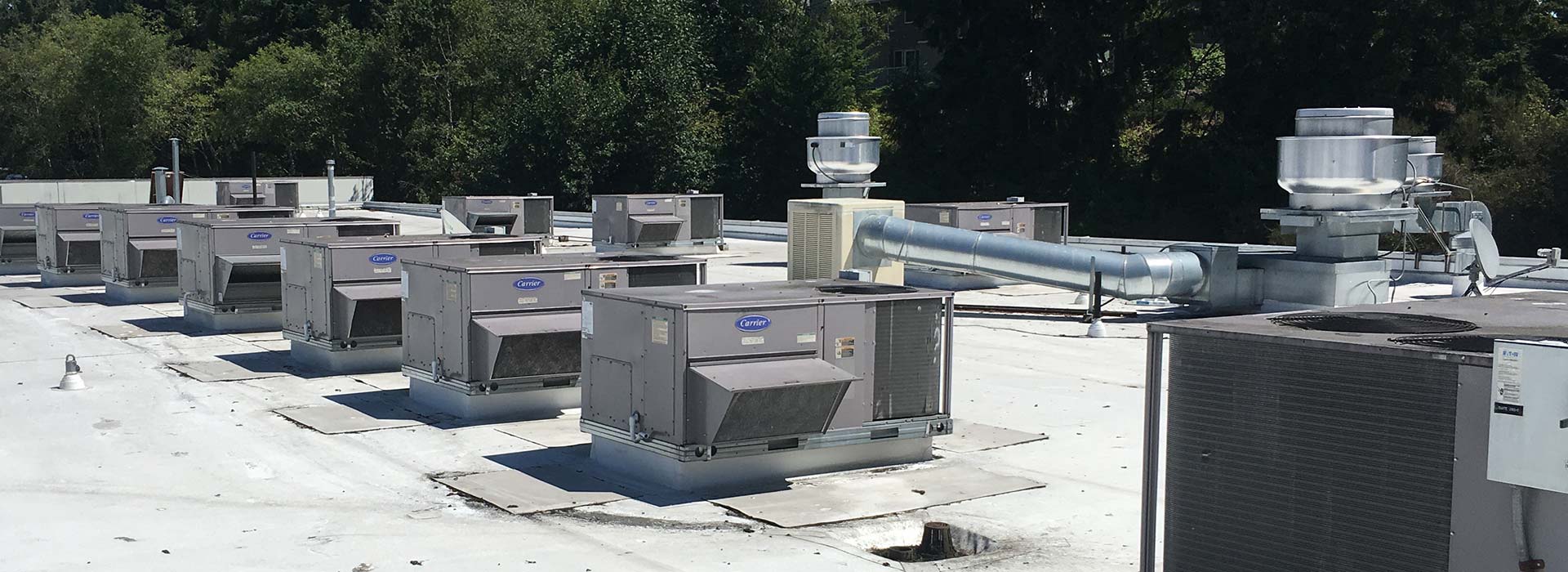
Commercial HVAC Maintenance
Heating and cooling systems work 7 days a week so regular care is needed to keep them from breaking down and costing you business. North Star Heating has over 30 years of experience servicing all brands of commercial HVAC equipment to keep it performing at its best.
- Our service area includes all businesses in Snohomish, Skagit, Whatcom and Island Counties.
- Our custom preventative maintenance plans are tailored to your specific equipment with service on a quarterly, seasonal or annual basis.
- Please note-we focus on commercial maintenance and do not offer residential service.
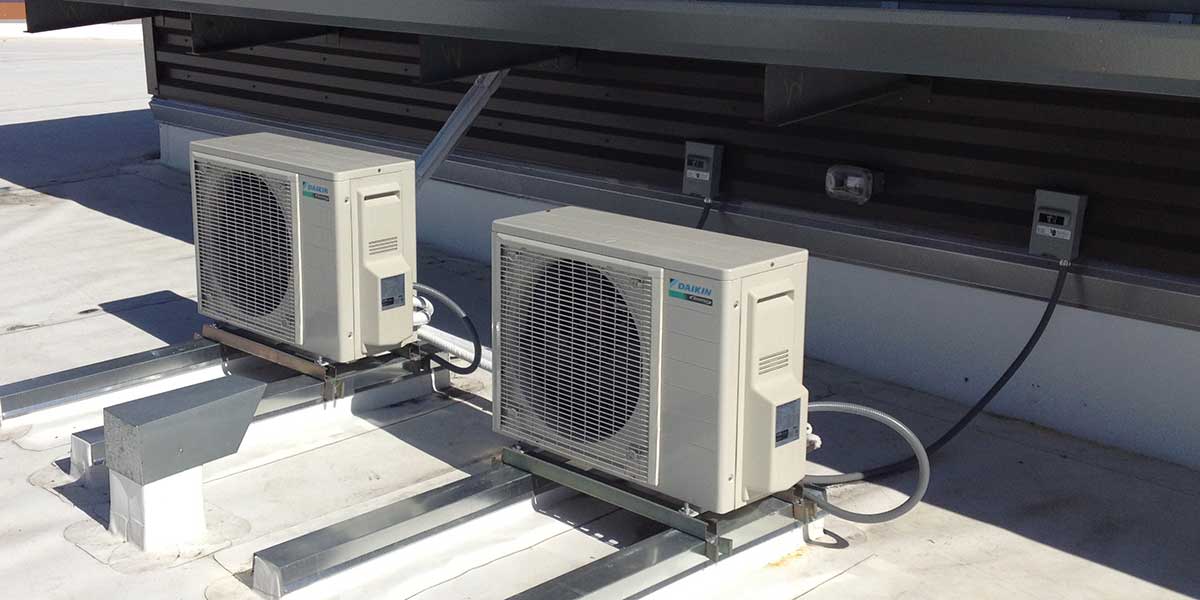
Custom maintenance plans
Our maintenance contracts offer yearly, seasonal or quarterly inspections for your equipment. Your preventative maintenance plan will include inspecting all equipment for potential issues along with checking and testing components to ensure they are working properly.
Any repairs found during our inspection will be written on a “QUOTE” form and submitted to you for approval. Our goal is to find any problems early and repair them while small and less expensive to fix.
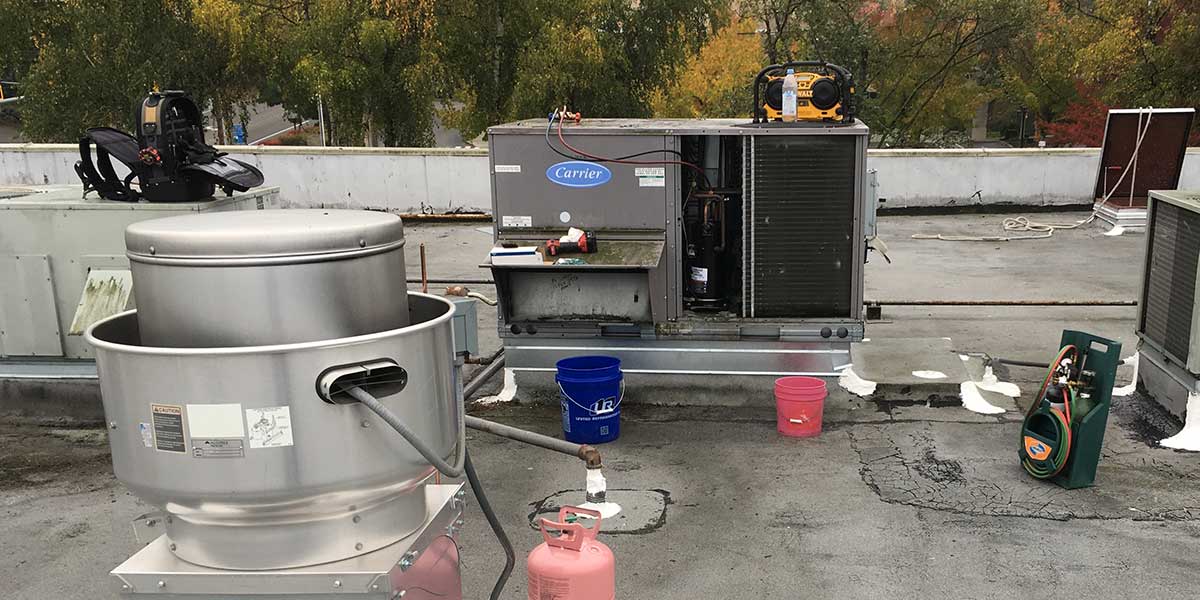
Why do you need preventative maintenance?
- Keep equipment running at maximum efficiency
- Identify problems when small & cost less to fix
- Reduce down time & emergencies
- Extend the life of your equipment
Quarterly HVAC maintenance items
This is a partial list of quarterly maintenance items, which varies depending on your equipment.
- Replace air filters/clean washable air filters
- Inspect indoor/outdoor coils & hand brush as needed
- Check fresh air inlet screens
- Inspect belts, sheaves, pulleys, fan blades, etc.
- Check motor/blower shaft bearings & contactors/relays for wear
- Inspect circuit boards, electrical disconnect switches & fuses
Annual heating & cooling inspection
This is a small sample of components tested and checked annually, which is customized based upon your existing equipment.
- Inspect heat exchangers, burners & gas valve operation
- Check all controls & adjust if necessary
- Test safety devices to ensure proper operation
- Tighten all electrical connections in control panels
- Check refrigerant operating pressures
- Confirm all Schrader caps are snug & in place
Commercial HVAC plans pay off
Regular maintenance of your heating and cooling equipment keeps it operating at maximum efficiency, which results in the following:
Contact us to learn more about how we can keep your commercial equipment running its best while avoiding the added stress of unwanted breakdowns.
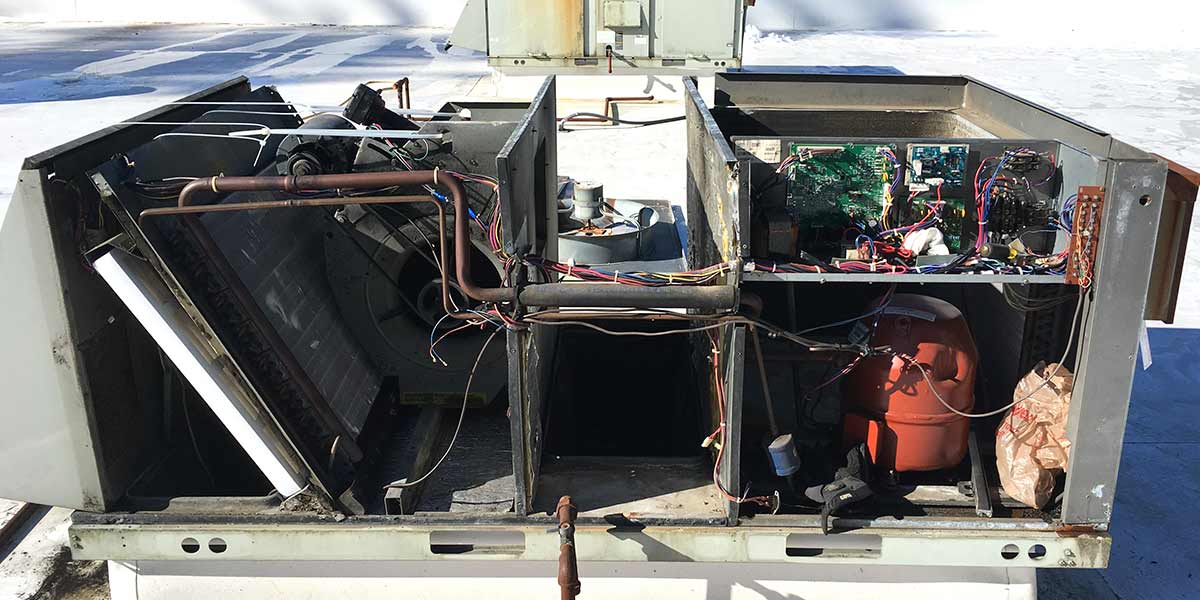
Decreased energy consumption
Means you save money on monthly bills which can add up fast.
Extended lifespan of equipment
Another money saver as you won't have to replace equipment as soon.
Reduced risk of refrigerant leaks
Less chance of potential ozone damaging refrigerant leaks.